A brief overview of die casting
Die casting is a metal casting process that uses reusable molds called dies to produce accurately shaped metal parts at high volumes. In the die-cast process, the mold is made from tool steel and has two halves. The molten metal, usually a non-ferrous alloy, is injected into the die under high pressure and held until it solidifies.
The die-cast zinc process is characterized by its speed, high productivity, and ability to make complex shapes with good dimensional accuracy and smooth surfaces. Parts made by die-casting aluminum include automotive components like pedals, steering columns, and wheels. Other applications include housing for power tools, appliances, toys, and industrial machinery parts. Die-casting companies often employ this efficient manufacturing method ideal for high-volume production because the molds can be reused often. It produces components with closer tolerances and lower porosity than other casting techniques. The main advantages are fast production rates, consistency, and low labor costs per part produced.
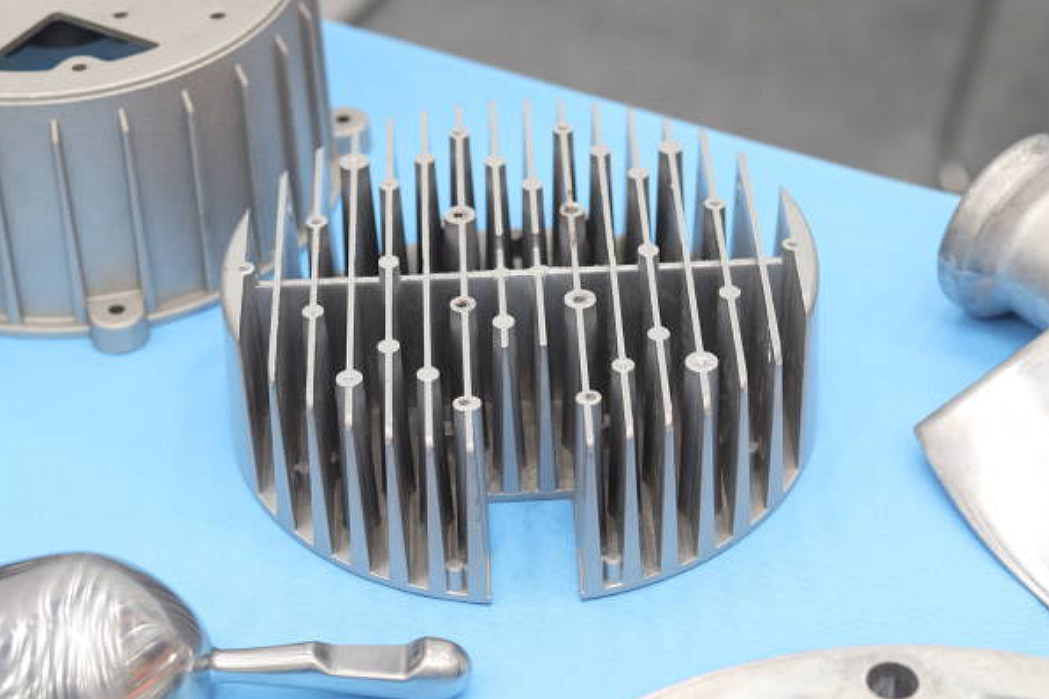
Two Main Types of Die Casting Processes
Hot chamber die casting is faster but limited in alloy choice, while cold chamber die casting is slower but more flexible with alloy selection. The type used depends on factors like cast metal, production volume, and part size.
Hot Chamber Die Casting
The die-cast process is a method used to produce metal parts with high precision and accuracy. It is primarily used for metals with low melting points, such as zinc, tin, and lead-based alloys. This process is commonly employed in producing small to medium-sized parts, including automotive components, electronic housings, and various consumer goods. Such as zinc die casting caps, USB drive shell, etc
How hot chamber die casting works
1. Die Preparation: The die-cast process begins with creating two die halves, typically made from hardened tool steel. These die halves have cavities that define the shape of the desired metal part. One die half is stationary, while the other is movable.
2. Injection System: In the die-cast process, the injection system consists of a crucible and a gooseneck. The crucible holds the molten metal, and the gooseneck (a metal tube) is connected to the crucible and the sprue hole in the stationary die half.
3. Filling the Crucible: The crucible is filled with metal alloy, typically preheated to a specific temperature to keep it liquid during the casting process. The metal is chosen based on the desired properties of the final product.
4. Melting and Injection: The gooseneck, immersed in the molten metal, acts as a channel to deliver the molten metal from the crucible to the die cavity. Powered by hydraulic or mechanical pressure, a piston forces the molten metal into the die cavity through the gooseneck. This pressure is maintained until the metal solidifies in the die.
5. Cooling and Solidification: Once the molten metal is injected into the die cavity, it rapidly cools and solidifies, taking the shape of the cavity. The cooling process is precisely controlled to ensure the metal solidifies uniformly and without defects.
6. Ejection: After the metal has solidified, the movable die half is opened, and the solidified part is ejected from the die cavity using ejector pins. The part is then removed from the machine for further finishing processes, such as trimming excess material and surface finishing.
7. Repeating the Process: The die-cast process can be automated and repeated continuously, allowing for high-volume production of identical metal parts.
Advantages of Hot Chamber Die Casting
Hot chamber die casting is a versatile and efficient manufacturing process that offers numerous advantages, especially for producing small to medium-sized parts with complex shapes and high-quality surface finishes.
1. Faster Production Cycles: Hot chamber die casting involves injecting molten metal directly into the die cavity, eliminating the need to pre-fill the injection chamber with each cycle. This results in faster production cycles than cold chamber die casting, where the injection chamber must be filled with molten metal before each shot.
2. Excellent Surface Finish: The process allows for precise control of the molten metal flow and cooling, leading to superior surface finish and high-quality detailing on the final product. It makes hot chamber die casting suitable for parts that require smooth and aesthetically pleasing surfaces.
3. High-Dimensional Accuracy: Hot chamber die casting enables the production of complex and intricate shapes with tight tolerances. The high-pressure injection ensures that the molten metal fills the entire die cavity uniformly, resulting in parts with high dimensional accuracy.
4. Reduced Material Waste: The automated nature of hot chamber die casting allows for efficient material usage, as the molten metal is injected directly into the die cavity without excess material. It reduces material waste and makes the process more cost-effective for high-volume production.
5. Good Mechanical Properties: Parts produced through hot chamber die casting often exhibit good mechanical properties due to the fast cooling rates. It results in parts with desirable strength and structural integrity, making them suitable for various applications.
6. Suitable for Thin-Walled Parts: Hot chamber die casting is well-suited for manufacturing thin-walled parts with consistent thickness. The precise injection process ensures that the molten metal fills even the most minor sections of the die cavity, leading to uniform wall thickness.
7. Automation and Efficiency: Hot chamber die-casting machines can be automated easily, allowing continuous and high-volume production. The automated process reduces labor requirements, increases production efficiency, and minimizes the risk of human error.
8. Cost-Effective for Small to Medium-Sized Parts: Hot chamber die casting is often more cost-effective than other small to medium-sized parts manufacturing methods. It balances production speed, material usage, and part quality well.
9. Reduced Post-Processing: The high accuracy and quality achieved in hot chamber die casting often result in minimal post-processing requirements. It can lead to cost savings and faster time-to-market for the final products.
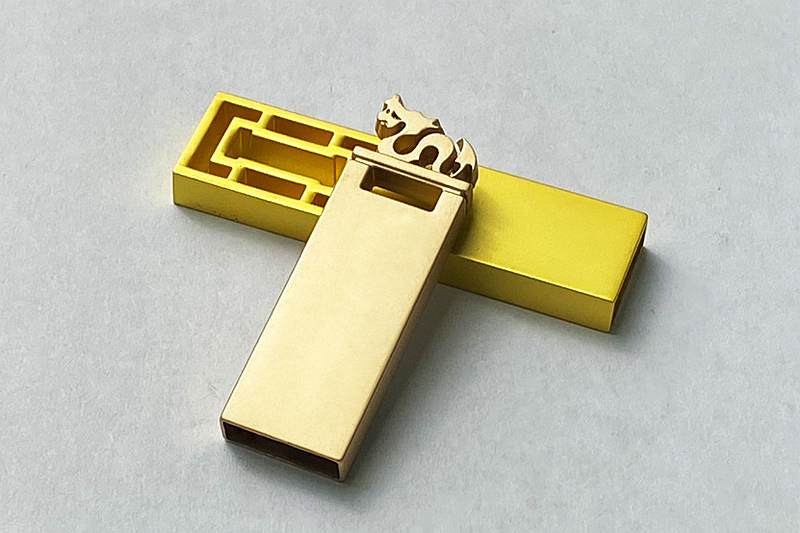
Limitations of hot chamber die casting
While hot chamber die casting offers various advantages, it has limitations and constraints that may make it unsuitable for specific applications. Despite these limitations, hot chamber die casting remains a valuable and widely used manufacturing process for specific applications, tiny to medium-sized, intricately shaped, and high-volume production parts made from compatible low-melting alloys. We should carefully consider the specific requirements of their parts before deciding on the appropriate casting method. Here are some of the main limitations of the hot chamber die-casting process:
1. Limited to Low-Melting Alloys: Hot chamber die casting is primarily suitable for metals and alloys with low melting points, such as zinc, tin, and lead-based alloys. High-melting-point materials, like aluminum and copper alloys, cannot be used in hot chamber die casting due to the risk of damaging the equipment and the short die life caused by the high temperatures.
2. Limited Part Size: Hot chamber die casting is generally more suitable for producing small to medium-sized parts. The size of the die-casting machine and the limitations of the hot chamber injection system can restrict the production of larger and heavier parts.
3. Corrosive Effects on Equipment: Some low-melting-point alloys used in hot chamber die casting, such as zinc-aluminum alloys, can be corrosive to the equipment over time. This corrosion can lead to increased maintenance and replacement costs for the machinery.
4. Less Control over Cooling Rates: Compared to cold chamber die casting, the cooling rates in hot chamber die casting are generally faster. While this can be advantageous for specific applications, it may also result in reduced control over the microstructure of the cast parts, potentially affecting their mechanical properties.
5. Limited Strength and Toughness: Parts produced through hot chamber die casting may have different mechanical strength and toughness than parts produced through other methods like cold chamber die casting or machining. This limitation can impact the suitability of hot chamber die casting for applications requiring high-strength components.
6. Uneven Heat Distribution: Due to the high temperatures, there is a risk of uneven heat distribution in the die, which can lead to thermal fatigue and premature die failure. It can result in additional maintenance and replacement costs for the dies.
7. Surface Defects: The fast cooling rates in hot chamber die casting can sometimes lead to surface defects such as air traps, cold shuts, or shrinkage porosity. Although these defects can often be mitigated through process optimization, producing high-quality parts remains a potential challenge.
8. Limited Alloy Flexibility: Hot chamber die casting is not as versatile in material selection as sand casting or investment casting. Hot chamber die casting may not be ideal if a specific part requires a different alloy with unique properties.
Cold Chamber Die Casting
The molten metal is held in a separate reservoir outside the machine in cold chamber die casting. The injection system is not submerged in the metal. When ready, a vacuum assist draws the molten metal into a gooseneck barrel, and the plunger injects it into the die under high pressure. The die is separate from the injection system. Cold chamber die casting can use metals with higher melting points, such as aluminum, copper, and magnesium alloys. Cycle times are slower than the hot chamber, but the separation of melt from the plunger allows for a broader range of alloys.
How cold chamber die casting works
1. Die Preparation: The die-cast process begins with creating two die halves, typically made from hardened tool steel. These die halves have cavities that define the shape of the desired metal part. One die half is stationary, while the other is movable.
2. Metal Melting: The metal is melted in a separate furnace outside the casting machine in the cold chamber die-casting process. The furnace is designed to handle the high temperatures required to melt materials with higher melting points. Once the metal reaches the proper temperature, a ladle or automated system transfers the molten metal into the cold chamber of the die-casting machine.
3. Injection System: The cold chamber of the die-casting machine contains a piston or plunger that acts as an injection system. The molten metal from the furnace is poured into the cold chamber, and the plunger is used to force the metal into the die cavity.
4. Filling the Die Cavity: When the plunger pushes the molten metal into the die cavity, it fills all the intricacies and cavities of the die, taking the shape of the desired part. High pressure is applied to ensure complete filling and minimize defects in the final product.
5. Cooling and Solidification: Once the die cavity is filled with molten metal, the metal rapidly cools and solidifies within the die. The cooling process is precisely controlled to allow the part to solidify uniformly and acquire the desired mechanical properties.
6. Die Opening and Ejection: After the metal has solidified and cooled sufficiently, the movable die half is opened, and the solidified part is ejected from the die cavity. Ejector pins or other mechanical means remove the part from the die. The die is then ready for the next casting cycle.
7. Trimming and Finishing: Once the part is ejected from the die, it may undergo further finishing processes, such as removing excess material (trimming), CNC machining, or surface treatments, to achieve the final required specifications and appearance.
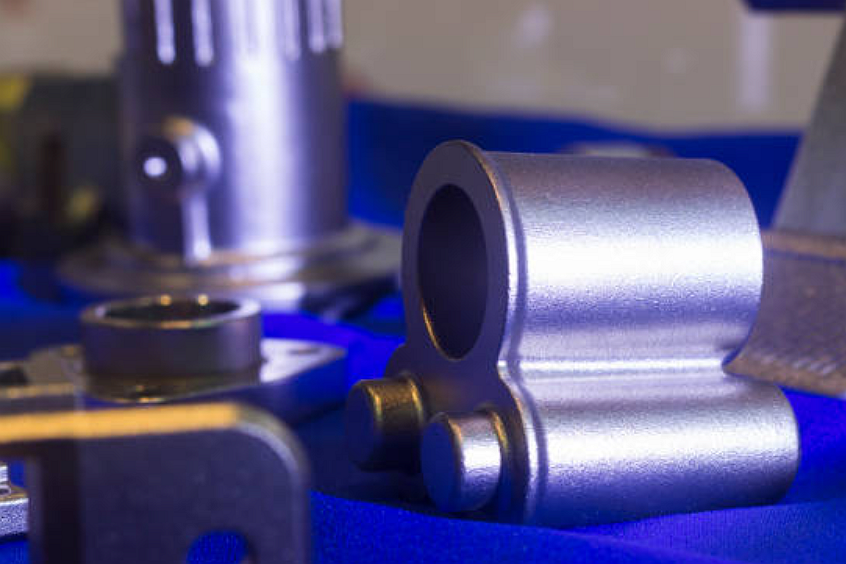
8. Repeating the Process: The cold chamber die-casting process can be automated and repeated continuously, allowing for high-volume production of identical metal parts.
Advantages of cold chamber die casting
Cold chamber die casting offers several advantages, making it a preferred manufacturing method for specific applications, especially for metals with higher melting points. Cold chamber die casting is a versatile and efficient manufacturing process that offers numerous advantages, especially for producing parts made from high-melting-point alloys and more significant components with stringent mechanical requirements. Here are some of the critical advantages of the cold chamber die-casting process:
1. Suitable for High-Melting-Point Alloys: One of the most significant advantages of cold chamber die casting is its ability to handle metals and alloys with high melting points, such as aluminum, copper, and alloys. It makes it ideal for producing parts with desirable mechanical properties and strength.
2. Superior Mechanical Properties: Parts produced through cold chamber die casting often exhibit excellent mechanical properties, including higher tensile strength, toughness, and fatigue resistance. The controlled cooling rates in the process contribute to the improved mechanical characteristics of the final products.
3. Ideal for Larger and Heavier Parts: Cold chamber die casting is well-suited for producing larger and heavier parts that require a substantial amount of molten metal. This capability makes it a preferred choice for manufacturing engine components, transmission parts, and other automotive and industrial components.
4. Longer Die Life: Compared to hot chamber die casting, where the die is exposed to the corrosive effects of certain low-melting alloys, cold chamber die casting involves a separation between the melting furnace and the die casting machine. This separation reduces the wear and corrosion on the dies, leading to die life longer and reduced maintenance costs.
5. Less Porosity and Better Surface Finish: The controlled cooling and solidification process in cold chamber die casting reduces porosity in the final parts, leading to higher density and better overall structural integrity. The process typically yields parts with smoother surface finishes, reducing the need for additional post-processing.
6. High-Dimensional Accuracy and Consistency: Cold chamber die casting allows for precise control over the metal flow and cooling rates, leading to parts with high dimensional accuracy and consistency. It makes it suitable for applications where tight tolerances and precise fit are critical.
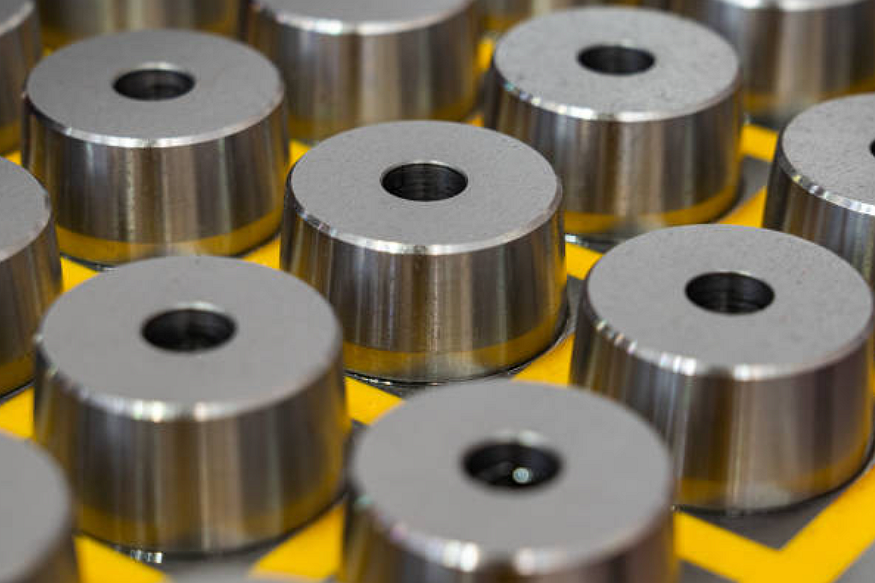
7. Reduced Flash Formation: Flash is an unwanted thin layer of excess metal that can form along the parting line of the die during the casting process. Cold chamber die casting generally produces less flash than other casting methods, reducing the need for trimming and further finishing operations.
8. Better Heat Dissipation: Cold chamber die casting's controlled cooling process allows for efficient heat dissipation during solidification, which can benefit parts that require good thermal conductivity.
9. Automation and Efficiency: Cold chamber die-casting machines can be automated easily, allowing continuous and high-volume production. This automation reduces labor requirements, increases production efficiency, and ensures consistent part quality.
Limitations of cold chamber die casting
While cold chamber die casting offers several advantages, it also has some limitations and challenges that should
Be considered when choosing the appropriate manufacturing method for a specific application. Despite these limitations, cold chamber die casting remains a valuable and widely used manufacturing process for producing high-quality metal parts, especially those made from high-melting-point alloys and more significant components with stringent mechanical requirements.
1. Slower Production Cycle: Compared to hot chamber die casting, cold chamber die casting typically involves a more complex setup due to the need for a separate melting furnace and metal transfer. It can result in slower production cycles, potentially affecting the overall production efficiency.
2. Higher Equipment and Energy Costs: Using a separate melting furnace and handling high-temperature alloys in the cold chamber die-casting process can lead to higher initial equipment costs. Additionally, operating the melting furnace requires significant energy consumption, which can add to the production expenses.
3. More Complex Setup and Handling: Cold chamber die casting involves additional steps and handling of molten metal from the furnace to the die casting machine. This complexity requires skilled operators and adds to the safety precautions of handling high-temperature alloys.
4. Limited to High-Melting-Point Alloys: While cold chamber die casting is suitable for high-melting-point alloys, it is not ideal for low-melting alloys, such as zinc and tin-based alloys, which are better suited for hot chamber die casting. This limitation can restrict the range of materials available for specific applications.
5. Limited Design Flexibility: Cold chamber die casting may not be as well-suited for complex and intricate part designs as other casting methods, like investment casting or sand casting. The high pressure in the process can make it challenging to produce parts with thin walls and intricate features.
6. Risk of Porosity: Although cold chamber die casting generally produces parts with reduced porosity compared to other casting methods, it is still possible to encounter porosity issues, particularly in thicker sections of the part. Proper design considerations and process optimization are necessary to minimize porosity.
7. Die Cost and Maintenance: Cold chamber die casting requires robust, durable dies capable of withstand high pressures and temperatures. These specialized dies can be more expensive to manufacture and maintain than other casting processes.
8. More Wasteful for Small Production Runs: The setup and preparation required for cold chamber die casting can make it less cost-effective for small production runs or prototypes. Other manufacturing methods like machining or rapid prototyping may be more suitable for such scenarios.
9. Surface Defects: While cold chamber die casting generally produces parts with good surface finish, specific complex geometries and material characteristics can lead to surface defects like flash or cold shuts, requiring additional post-processing steps.
Comparison Between Hot and Cold Chamber Die Casting
Hot chamber dies casting is faster and lower cost but material-limited, while cold chamber is slower and higher cost but more flexible with alloy choice. Here is a comparison between hot chamber and cold chamber die casting:
Molten Metal Source:
Hot chamber: Molten metal is held in a pool inside the machine's heated chamber. The injection system is submerged in this pool.
Cold chamber: Molten metal is held externally in a separate furnace. Metal is ladled into an unheated chamber.
Metal Temperature:
Hot chamber: Metal is held at a high temperature, keeping it molten between cycles.
Cold chamber: Metal is injected when needed and solidifies in the unheated chamber after each cycle.
Cycle Time:
Hot chamber: Cycle times are faster, usually less than 60 seconds.
Cold chamber: Cycle times are slower, around 60-120 seconds.
Metal Alloys:
Hot chamber: Limited to low melting point alloys like zinc, tin, and lead. Max temp ~1100°F.
Cold chamber: Can use higher melting point alloys like aluminum, magnesium, and copper.
Die Construction:
Hot chamber: Dies are attached to the heated machine chamber, made of cast iron or tool steel.
Cold chamber: Dies are separate from the injection system. They are usually made of tool steel.
Cost:
Hot chamber: Lower machine and die costs.
Cold chamber: Higher machine and die costs.
Automation:
Hot chamber: More manual labor intensive.
Cold chamber: Easier to automate.
When to Choose Hot or Cold Chamber Die Casting?
In general, hot chamber die casting works best for high volumes of small, simple parts that can tolerate looser tolerances. The cold chamber is preferred for more extensive, complex components made with higher melting point alloys, especially when lower volumes are required. Here are some guidelines on when to choose hot chamber or cold chamber die casting:
Hot Chamber Die Casting is best for
High-volume production of small, simple parts
Parts with thin walls and complex geometries
Alloys with low melting temperatures like zinc, tin, lead
Lower per-part tooling costs
Faster cycle times
Cold Chamber Die Casting is best for:
Lower to medium production volumes
Larger, thicker castings
Alloys with higher melting temperatures like aluminum, magnesium, brass
Vertical die orientation is required
Superior mechanical properties are needed
Automation is required
Extensive core pulling is needed
Key Factors to Consider
Number of castings required
Complexity and size of parts
Alloy to be die cast
Tolerance and surface finish requirements
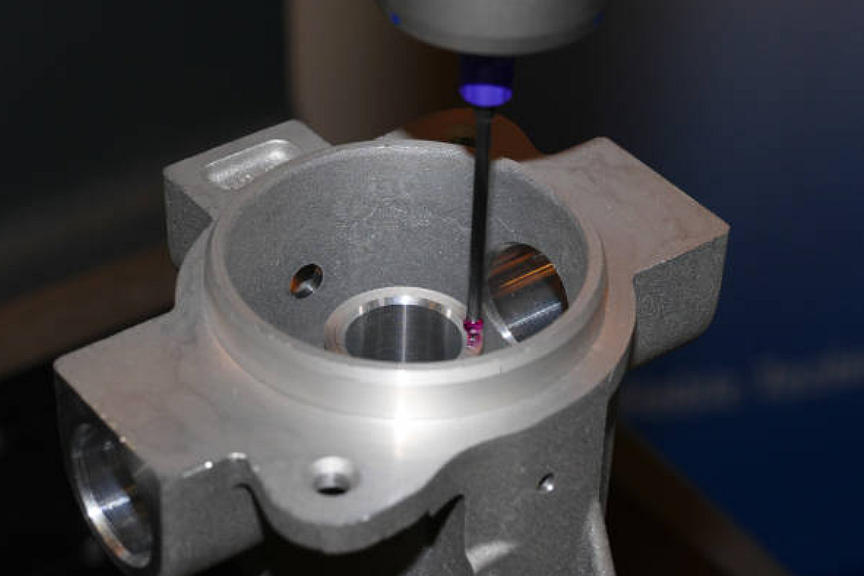
Production rate needed
Budget for tooling and equipment
Why Choose Us?
Hey there! Did you know Neway has been crafting custom metal, ceramic, and plastic parts for over 30 years? As experts in injection molding, die cast process, die casting, precision casting, and more; they've mastered it all. They want to help you turn your wildest ideas into reality with their non-standard manufacturing services. New customers get 20% off their first order in 2023! So what are you waiting for? Partner with Neway and make something unique.
评论
发表评论