Due to its high productivity, precision, and near-net-shape capabilities, The aluminum die-casting process is used extensively in the automotive, aerospace, and consumer products industries. However, defects can arise during the aluminum die-casting process that compromises the quality and performance of the cast components. This article will examine some of the most prevalent aluminum die-casting defects, their causes, impact, and mitigating solutions.
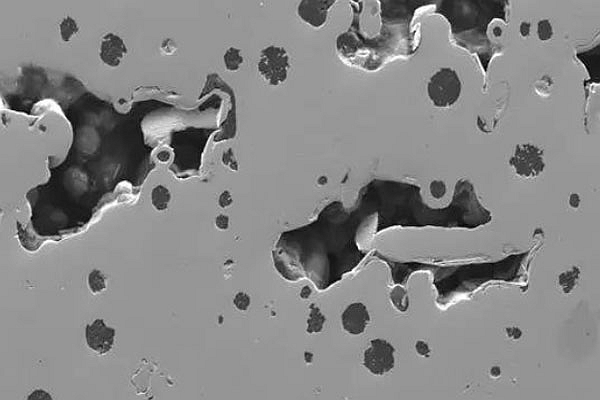
Avoiding defects is imperative for cost-effective, high-quality aluminum die-casting production. Careful analysis of alloy selection, die design, process control, and simulation is needed to proactively identify and address potential defects. Understanding the root causes and mitigation strategies for ordinary aluminum die-casting defects enables the manufacture of dimensionally accurate, structurally sound components. With sufficient upfront engineering rigor, aluminum die castings can provide exceptional performance and reliability.
Porosity and Air Entrapment
Porosity and air entrapment are some of the most frequently encountered defects in aluminum die castings, appearing as tiny holes or voids distributed within the part.
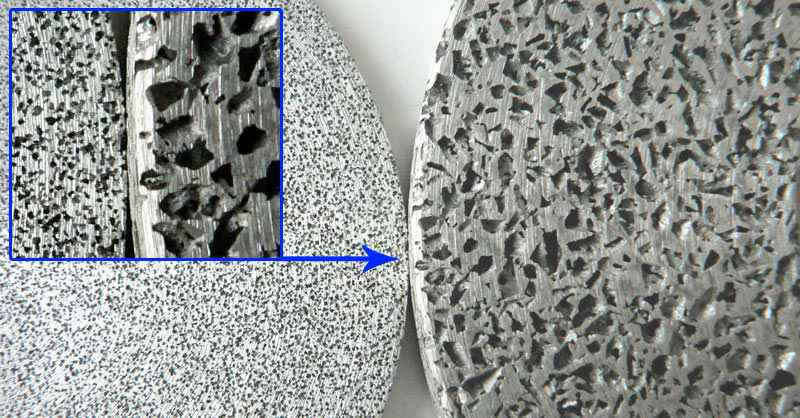
Causes: Excessive melt temperatures can cause air absorption and dissolve hydrogen, resulting in porosity. Inadequate venting restricts the escape of gases as the melt fills the die. Poor gating design leads to turbulent die-filling, trapping air bubbles.
Impact: Porosity weakens the part, acts as a stress concentrator, and impairs pressure tightness. Leaks, dimensional instability, loss of mechanical properties, and field failures can result.
Solutions: Optimizing the gating system design, vent placement, and die-fill dynamics can minimize air entrainment. Controlling melt temperature, covering fluxes, and degassing techniques reduce dissolved gases. Upfront simulation helps avoid problems.
Shrinkage and Microporosity
Solidification shrinkage and microporosity are also prevalent die-casting defects caused by inadequate feed metal to compensate for volumetric shrinkage.
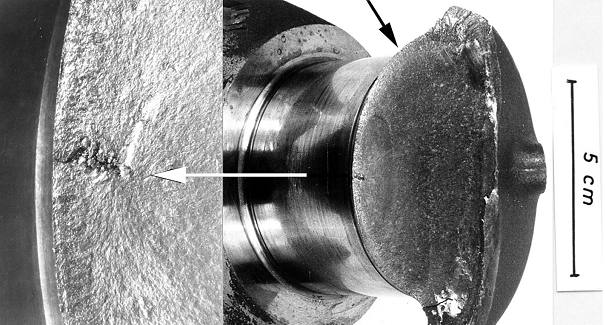
Causes: High cooling rates in die casting can lead to microporosity as solidification fronts meet before shrinkage voids are filled. Alloy sensitivity, thick sections, and poor venting aggravate these defects.
Impact: Reduced mechanical properties, loss of pressure tightness, potential leakage, and corrosion result from shrinkage. Microporosity weakens parts and reduces ductility.
Solutions: Adjusting gating to provide adequate metal volume, optimizing thermal gradients, and using squeeze pins can help compensate for shrinkage. Proper mold design, uniform cooling, modified alloys, and microstructure control minimize microporosity.
Cold Shut and Misruns
Cold shut and misrun defects derive from incomplete die cavity filling during casting.
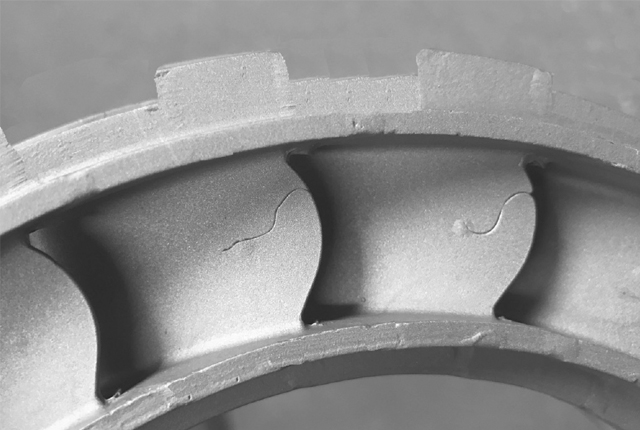
Causes: Low metal temperature or excessive cooling may prevent molten metal from reaching all die areas. Incorrect gating, premature solidification, gas entrapment, and poor venting promote these defects.
Impact: Cold shuts and misruns create weak spots and planes of discontinuity in castings, critically reducing strength and enabling component failures.
Solutions: Enhancing die lubrication and maintaining optimal pouring temperature help avoid these defects. Runner and gate size, number, and placement modifications improve cavity filling.
Flash and Flash Lines
Flash describes excess metal extruding from the parting line of the die during casting. Flash lines are unwanted ridges of solidified metal left on the casting.
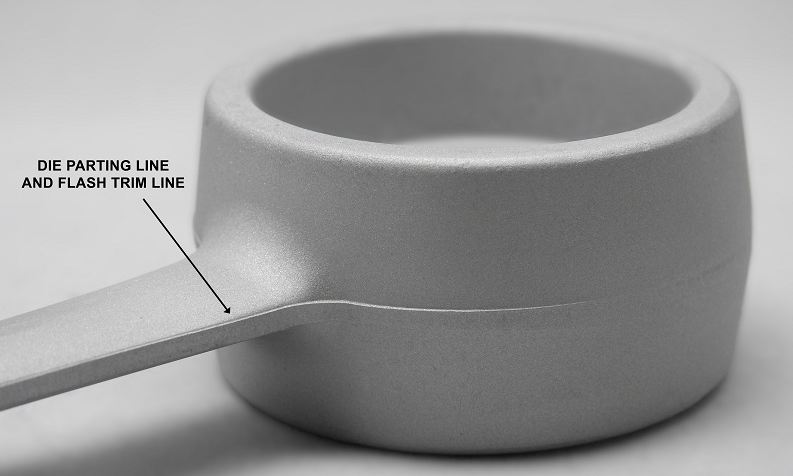
Causes: Improper clamping, uneven die expansion, particulate contamination, and worn die components can cause flash defects during casting by allowing seepage.
Impact: Flash must be removed by grinding, which is costly and time-consuming. It also indicates potential inadequacies in process control.
Solutions: Maintaining required clamping forces, replacing worn dies, improving die lubrication, and adjusting flash space dimensions help avoid flash. Controlling fill rate, metal temperature, and machine parameters is critical.
Hot Cracks and Tears
Hot cracks and tears appear as separations in the casting resulting from stresses during solidification.
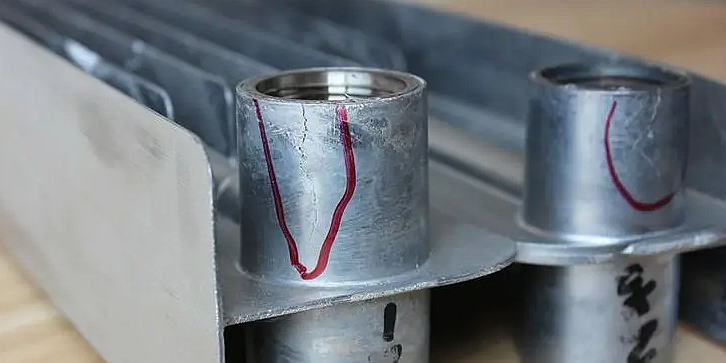
Causes: Constraints from the mold during solidification combined with high thermal gradients promote these defects in susceptible alloys. Poor gating design also contributes.
Impact: Cracks critically undermine cast components' integrity and longevity, leading to failures or inability to meet functionality requirements.
Solutions: Adjusting the gating design, controlling mold temperature, reducing thermal gradients, and using squeeze pins can help prevent hot tears. Optimizing cooling patterns and rates is imperative.
评论
发表评论