What is Ceramic Injection Molding (CIM)
Ceramic Injection Molding (CIM) is a manufacturing process used to produce complex and precise ceramic components. It is based on traditional plastic injection molding and sintering process principles but is adapted for ceramics, which are inherently more rigid and brittle materials.
The CIM process involves the following steps:
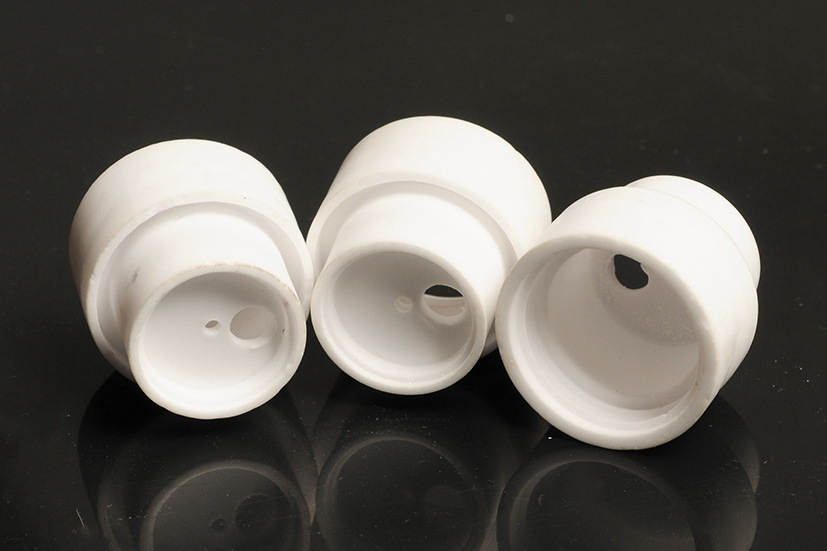
1. Feedstock Preparation: Ceramic powders are mixed with binders and other additives to create a homogeneous feedstock. The binders make the mixture more pliable and suitable for ceramic injection molding.
2. Injection Molding: The prepared feedstock is injected into a mold cavity under high pressure and temperature using an injection molding machine. The mold is typically steel and designed to shape the final ceramic part.
3. Debinding: The green ceramic part still contains the binders after injection molding. The molded parts are subjected to a debinding process, where the binders are removed either thermally (thermal debinding) or chemically (solvent debinding).
4. Sintering: Once the binders are removed, the green parts are subjected to a high-temperature sintering process in a furnace. Sintering causes the ceramic particles to fuse, resulting in a fully dense and high-strength ceramic component.
5. Post-Processing: After sintering, additional finishing processes like polishing, grinding, or CNC machining may be employed to achieve the desired final dimensions and surface quality.
Ceramic Injection Molding (CIM) service offers several advantages over traditional ceramic processing methods, including the ability to produce intricate shapes with high precision and repeatability. It also enables the mass production of complex ceramic parts with reduced costs and material waste. CIM is widely used in various industries, including electronics, Aerospace, medical, and automotive, where advanced ceramics are required for specific applications due to their excellent thermal, mechanical, and electrical properties.
Properties of Alumina CIM Parts
Exceptional Thermal Resistance
Alumina, or aluminum oxide (Al2O3), exhibits exceptional thermal resistance due to its crystal structure and ionic solid bonding between aluminum and oxygen atoms. Alumina is a ceramic material, and its crystal lattice has a unique arrangement that allows it to withstand high temperatures without significant structural changes or softening. The key factors contributing to Alumina's thermal resistance are:
High Melting Point: Alumina has a melting point of approximately 2,072 degrees Celsius (3,762 degrees Fahrenheit). It means it remains solid and retains its structural integrity at extremely high temperatures, well above those experienced in most industrial and engineering applications.
Strong Ionic Bonds: The bonding between aluminum and oxygen atoms in the alumina crystal structure is highly stable and robust. These strong ionic bonds prevent significant atomic movement even at elevated temperatures, leading to excellent thermal stability.
High Oxidation Resistance: Alumina forms a protective surface oxide layer when exposed to oxygen at high temperatures. This layer acts as a barrier, preventing further oxidation and enhancing the material's resistance to thermal degradation.
Minimal Thermal Expansion: Alumina has a relatively low coefficient of thermal expansion. It means that even when exposed to temperature changes, the material expands and contracts minimally, reducing the risk of thermal stresses that could lead to cracking or failure.
Why CIM Parts Suitable for High-Temperature Applications
The exceptional thermal resistance of Alumina makes CIM parts made from this material well-suited for high-temperature applications. Some of the key advantages include:
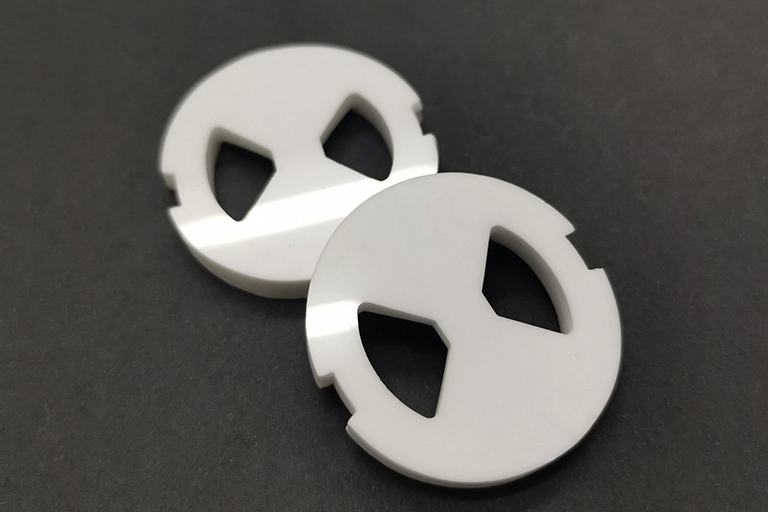
High-Temperature Stability: Alumina CIM parts can maintain their structural integrity and mechanical properties at elevated temperatures. They do not deform, soften, or undergo phase changes, ensuring reliable performance in demanding thermal conditions.
Resistance to Thermal Shock: Alumina's low coefficient of thermal expansion and high thermal conductivity enables it to withstand rapid changes in temperature without fracturing due to thermal shock. This property is particularly crucial in applications where quick heating or cooling occurs.
Heat Resistance in Industrial Environments: Alumina CIM parts can be used in industrial applications such as furnace components, heating elements, and thermal barriers, where exposure to high temperatures is expected.
Automotive and Aerospace Applications: Alumina CIM parts find use in automotive engines, aerospace components, and exhaust systems, where high-temperature environments are prevalent.
Mechanical Strength and Hardness
Alumina CIM parts exhibit superior mechanical properties compared to most other material options, making Alumina suitable for structural load-bearing applications. The high hardness provides excellent wear resistance as well. Alumina CIM parts have excellent mechanical strength and hardness properties compared to other materials used in ceramic injection molding:
Mechanical properties of Alumina CIM parts
Alumina has high flexural strength, typically over 300 MPa. It gives alumina CIM components excellent load-bearing capabilities under bending forces.
High strength: The material has a compressive strength exceeding 2,000 MPa. It allows alumina parts to withstand high loads without fracturing.
High hardness: Alumina has a Vickers hardness rating of 16-18 GPa, making it scratch and wear-resistant.
Reasonable fracture toughness: Though brittle, Alumina has reasonable fracture toughness (K1C 3-5 MPa√m) for a ceramic due to its fine grain structure.
High-temperature strength: Strength is retained even at temperatures up to 1,000°C.
Comparison with other materials used in CIM
CIM-ZAT: Alumina has 2-3 times higher flexural strength than zirconia toughened Alumina (ZTA) composites also used in CIM.
MIM-Metals: It has significantly better hardness and wear resistance than CIM parts made from metals like MIM-stainless steel or MIM-titanium alloys.
CIM- Advanced ceramics: Alumina has higher compressive and flexural strength than pure ceramics like silicon nitride and silicon carbide.
Engineering plastics: It matches/exceeds the strength of commonly used engineering thermoplastics like PEEK, PSU, and PPS in injection molding parts.
Excellent Wear Resistance
Alumina's outstanding wear resistance and other desirable properties make it an essential material in various industries where components are exposed to abrasive and high-stress environments. Its ability to withstand wear and maintain performance over time contributes to improved reliability, reduced maintenance, and longer component lifespans. Alumina exhibits excellent wear resistance due to its inherent mechanical properties and microstructural features. The key factors contributing to Alumina's wear-resistant characteristics include:
Hardness: Alumina is a tough material, second only to diamond on the Mohs scale. This high hardness makes it highly resistant to abrasion and wear when in contact with other materials, especially those with lower hardness.
Low Coefficient of Friction: Alumina has a relatively low coefficient of friction, which means it generates less frictional heat and experiences reduced wear when sliding or rubbing against other surfaces. This property is fundamental in applications involving high-speed and continuous motion.
Fine Microstructure: Alumina ceramics can be manufactured with fine-grained microstructures through advanced processing techniques. Fine-grained Alumina exhibits better wear resistance than coarser-grained ceramics, as it hinders the propagation of wear-related cracks and reduces surface damage.
High Compressive Strength: Alumina has a high compressive strength, allowing it to withstand compressive stresses without deformation. This strength helps prevent the occurrence of wear through surface indentation or deformation.
Chemical Inertness: Alumina is chemically inert and resistant to most chemicals, acids, and alkalis. This chemical stability protects the material from chemical wear and corrosion, making it suitable for aggressive environments.
Applications Where Wear Resistance is Critical:
Wear resistance is critical in various industrial applications where materials are subjected to friction, abrasion, and continuous contact with other surfaces. Some critical applications where Alumina's excellent wear resistance is precious include:
CIM-Alumina Cutting Tools: Alumina-based cutting tools are used in machining applications, such as turning, milling, and drilling, where they need to endure high-speed cutting, heat, and abrasive interactions with the workpiece.
CIM-Alumina Bearings and Bushings: Alumina bearings and bushings are utilized in various machinery and equipment, including pumps, compressors, and engines, to provide low-friction and long-lasting performance in high-load, rotating applications.
Ceramic Seals and Bearings for High-Temperature Applications: Alumina is used in high-temperature environments, such as in furnaces, kilns, and gas turbines, where it provides excellent wear resistance and dimensional stability under extreme thermal conditions.
Wear-Resistant Components for Automotive and Aerospace: Alumina-based components are used in automotive and Aerospace applications where resistance to wear and friction is crucial, such as in brake systems, engine components, and aerospace bearings.
Medical and Dental Implants: Alumina's wear resistance and biocompatibility make it a suitable material for medical and dental implants that require long-term durability and low wear in contact with tissues.
Electrical Insulation Properties
Alumina CIM parts leverage excellent electrical insulation properties to enable miniaturization and improved performance in electronics operating at high voltages, frequencies, and temperatures. Alumina has excellent electrical insulation properties that benefit electrical and Electrical insulating capabilities:
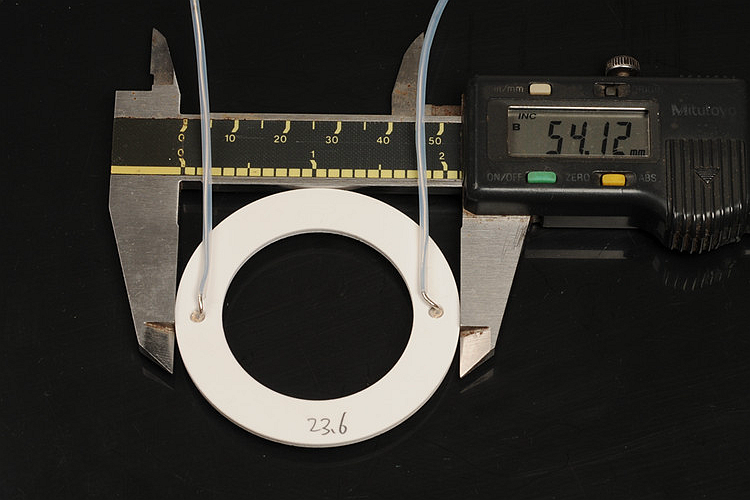
High electrical resistivity: Alumina has a very high electrical resistivity, around 10^14 ohm-cm at room temperature. It makes it an excellent electrical insulator.
High dielectric strength: It has a high dielectric strength of 15-35 kV/mm. It equates to a very high breakdown voltage that resists electrical failure.
Electrical insulation properties: Alumina maintains its electrical insulation properties at elevated temperatures. Its dielectric constant remains stable up to 1,000°C.
Low dielectric loss: The material has a low dielectric loss, meaning minimal leakage current flows through Alumina at high voltages or frequencies.
Good thermal conductivity: Alumina has good thermal conductivity for a ceramic, allowing heat dissipation in electrical devices.
Electrical and electronic CIM applications:
CIM insulator parts: Alumina CIM components can be used as insulators, spacers, and supports in high-voltage systems that operate at thousands of volts.
Ceramic sensors: Alumina provides electrical isolation in sensors for temperature measurement and control in industrial processes.
Alumina substrates: Alumina substrates facilitate mounting power semiconductor chips and integrated circuits without short-circuiting.
Chemical Stability
Alumina's inertness enables it to withstand extreme chemical conditions that rapidly degrade other materials, making it an ideal choice for highly corrosive applications. Alumina has excellent chemical corrosion resistance owing to its inert nature, making it suitable for highly aggressive chemical environments:
1. Alumina is highly stable and non-reactive with most acids, alkalis, organic solvents, and aqueous solutions at room temperature.
2. It forms a protective and regenerative oxide layer when exposed to oxidizing environments, preventing further chemical attacks.
3. Alumina has excellent resistance to wet corrosion from acids like sulfuric, nitric, and hydrofluoric acid, even at elevated temperatures.
4. It does not react with molten metals or glasses and is resistant to metal vapors like mercury, zinc, and sodium.
5. Alumina retains its mechanical strength in harsh chemical environments with minimal degradation over time.
Applications in chemically aggressive environments:
Industry valves: Components like pump impellers, valve balls, and tanks for handling caustic solid or acidic solutions.
Sensors and probes: Used in chemical reactors and downstream processing systems.
Applications of Alumina CIM Parts
Aerospace Applications
Advantages of using CIM Alumina parts in Aerospace Applications:
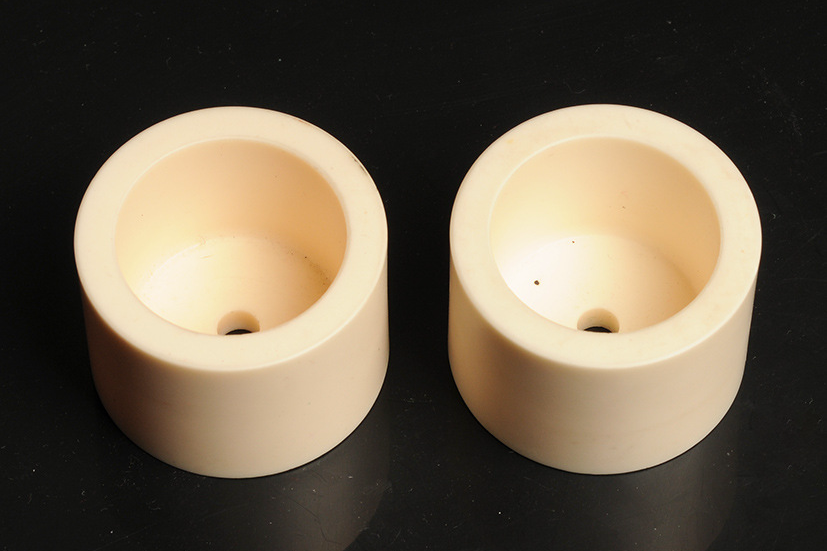
Lightweight: Alumina is a lightweight material, which is crucial in Aerospace to reduce the overall weight of components and enhance fuel efficiency.
High Strength and Stiffness: Alumina CIM parts offer excellent mechanical strength and stiffness, making them suitable for structural components that must withstand high loads and stresses.
High-Temperature Resistance: Alumina's exceptional thermal stability allows it to maintain its mechanical and electrical properties at elevated temperatures, making it suitable for aerospace applications in high-temperature environments.
Wear Resistance: Alumina's wear resistance is advantageous for aerospace components subject to abrasive conditions, such as bearings and seals.
Specific CIM Alumina Aerospace components:
Bearings: Alumina bearings provide low friction and high wear resistance, making them ideal for aerospace applications.
Seals and Gaskets: Alumina's chemical and thermal stability suits it for sealing applications in aerospace engines and other components.
Insulators: Alumina insulators are used in electrical components of aerospace systems to provide electrical isolation.
CIM Alumina Parts in Medical Devices
Biocompatibility and Medical-Grade Alumina CIM Parts: Alumina is biocompatible and well-tolerated by the human body, making it suitable for medical implants and devices.
Medical-grade Alumina is carefully processed to ensure it meets stringent standards for use in biomedical applications.
Examples of Medical Devices benefiting from Alumina Components:
Dental Implants: Alumina dental implants offer excellent biocompatibility and mechanical properties, making them a viable option for tooth replacements.
Joint Replacements: Alumina components, such as hip and knee joint replacements, provide wear resistance and durability for long-term medical applications.
Electronics and Electrical Engineering
Alumina as a Reliable Insulating Material in Electronics:
Alumina's excellent electrical insulating properties and high dielectric strength make it suitable for various electrical and electronic applications.
It creates insulators, substrates, and circuit boards for electronic devices.
Alumina Components Used in Electrical Engineering Applications:
Ceramic Substrates: Alumina substrates are used in electronic circuits for their electrical insulation and heat dissipation properties.
Insulating Spacers: Alumina spacers are used in electrical assemblies to maintain proper spacing and electrical isolation.
Automotive Sector
Alumina components improve automotive performance by reducing weight and enhancing wear resistance.
They contribute to better thermal management and electrical insulation in automotive systems.
Specific Automotive Applications of Alumina Components:
Automotive Bearings: Alumina bearings provide low friction and high wear resistance in automotive engines and other moving parts.
Brake Components: Alumina ceramics are used in brake systems to enhance performance and reduce wear.
Industrial Machinery
Alumina's Role in Improving the Efficiency and Longevity of Machinery:
Alumina components in industrial machinery provide wear resistance, reducing maintenance and extending the lifespan of the equipment.
They offer electrical insulation and thermal management, enhancing machinery performance and reliability.
Examples of Industrial Machinery Utilizing Alumina Parts:
Pumps and Valves: Alumina components are used in pumps and valves for their wear resistance and chemical stability.
Cutting Tools: Alumina-based cutting tools are employed in machining due to their wear resistance and ability to withstand high temperatures.
Why Choose Neway for CIM Parts
David Chen of Neway explains how alumina injection molded components outperform in extreme environments. "Alumina has remarkable properties like strength and hardness maintained to over 1000°C. It resists corrosion and wears incredibly well. We mold complex alumina geometries unattainable by other methods." Major industries turn to Neway's 30 years of experience. "We collaboratively design alumina parts for each customer's specific application, from aerospace nozzle inserts to biomedical implants. Get precisely net-shaped ceramics with tight tolerances." New customers can try Neway's capabilities with a 20% discount on initial orders of alumina parts.
评论
发表评论