In today's world of technological marvels, 3D printing has emerged as a groundbreaking innovation that has revolutionized how we create and manufacture objects. From rapid prototyping to complex medical implants, this cutting-edge technology has captured the imagination of engineers, designers, and artists alike. But what exactly is 3D printing, and how does it work? This article will explore the intricacies of the 3D printing process, delve into its various classifications, discuss the materials used, and uncover its vast applications.
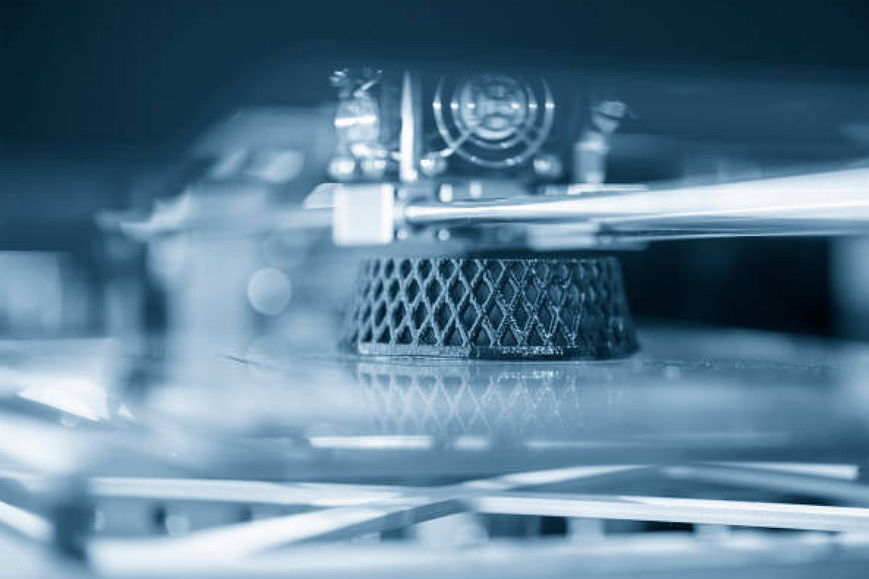
Understanding the 3D printing Process
At its core, 3D printing is an additive manufacturing technique that constructs three-dimensional objects layer by layer based on a digital design. Unlike traditional subtractive manufacturing methods, which involve cutting or carving away material from a solid block, 3D printing builds objects from scratch. The process involves several key steps that bring a digital concept into tangible reality.
Firstly, a digital design is created using computer-aided design (CAD) software or obtained from existing 3D models. This design serves as the blueprint for the object to be printed. Next, the design is sliced into numerous cross-sectional layers and sent to the 3D printer.
The 3D printing process begins with material deposition and solidification. Depending on the printing technology employed, this can involve the extrusion of molten plastic, the curing of liquid resin using ultraviolet light, or the sintering of powdered material with a laser. These layers gradually stack upon one another, eventually forming the complete object.
Post-processing and finishing are the final steps in the 3D printing process. This can include removing support structures, smoothing rough surfaces, or applying additional treatments like painting or polishing to achieve the desired aesthetics and functionality.
Classification of 3D Printing Technologies
Several distinct 3D printing technologies are available today, each with unique strengths and applications. Let's explore some of the most prominent ones:
Fused Deposition Modeling (FDM)
FDM is one of the most widely used 3D printing technologies. It extrudes thermoplastic filaments through a heated nozzle, solidifying as it cools down. FDM printers are relatively affordable and can produce robust, functional prototypes and end-use parts. However, the layer lines may be visible, affecting the surface finish.
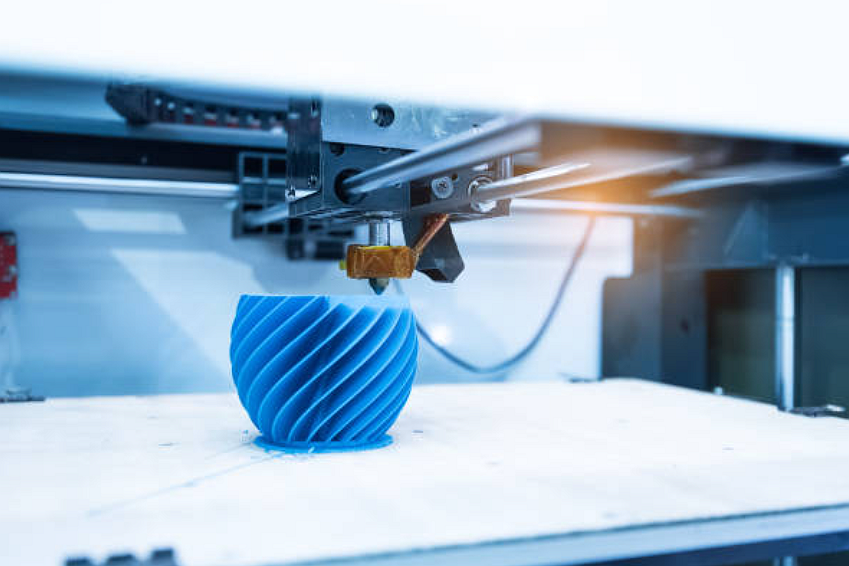
Stereolithography (SLA)
SLA employs a vat of liquid photopolymer resin and a laser to cure the resin layer by layer selectively. SLA printers are known for their high precision and ability to produce intricate details. This technology is often used in jewelry making, dental applications, and rapid prototyping industries.
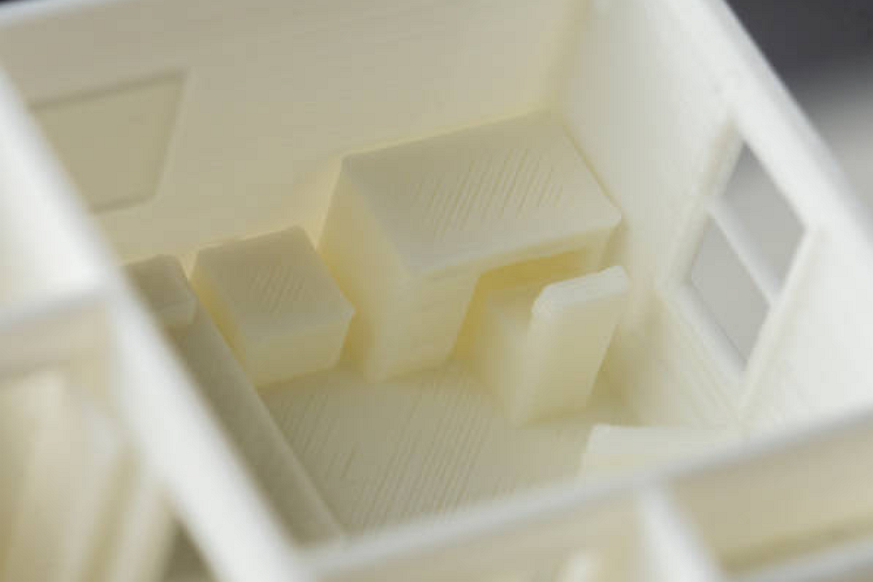
Selective Laser Sintering (SLS)
SLS employs a high-powered laser to fuse powdered materials, such as nylon or metal, into solid objects. The advantage of SLS lies in its ability to print complex geometries and functional parts with excellent mechanical properties. It finds applications in aerospace, automotive, and medical fields.
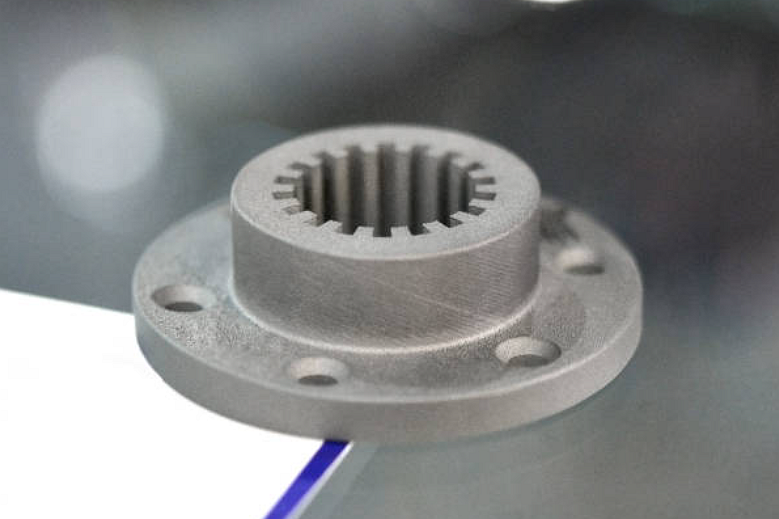
Digital Light Processing (DLP)
DLP technology utilizes a digital light projector to cure liquid resin, similar to SLA selectively. DLP printers can achieve faster print speeds than SLA, but the surface quality may be slightly lower. This technology is commonly used in dental applications, jewelry manufacturing, and consumer goods.
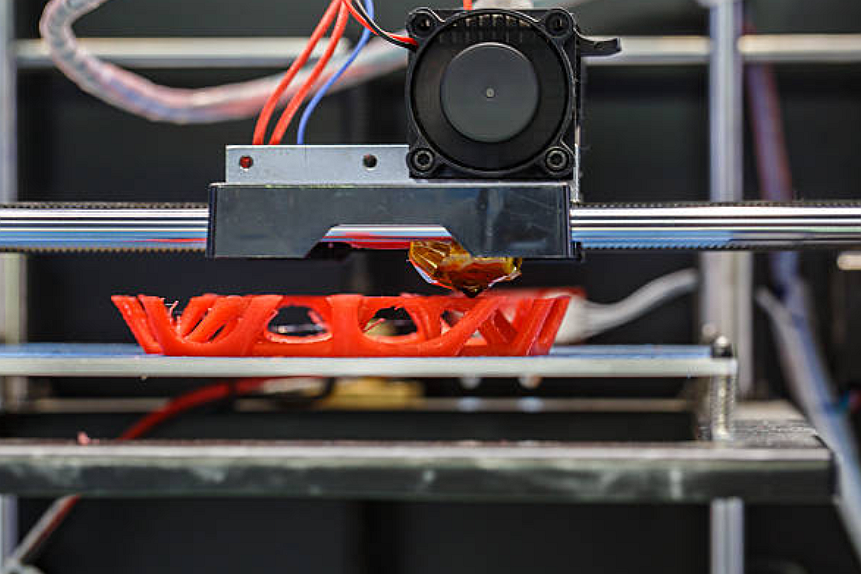
Multi Jet Fusion (MJF)
Multi Jet Fusion operates on the principle of selectively applying fusing and detailing agents to a bed of powdered material. The process begins with a thin layer of powdered material, typically nylon, spread evenly across the build platform. The print head then moves across the bed, jetting tiny fusing agent droplets onto the areas where fusion is desired. Simultaneously, a detailing agent is jetted to define specific features and enhance resolution.
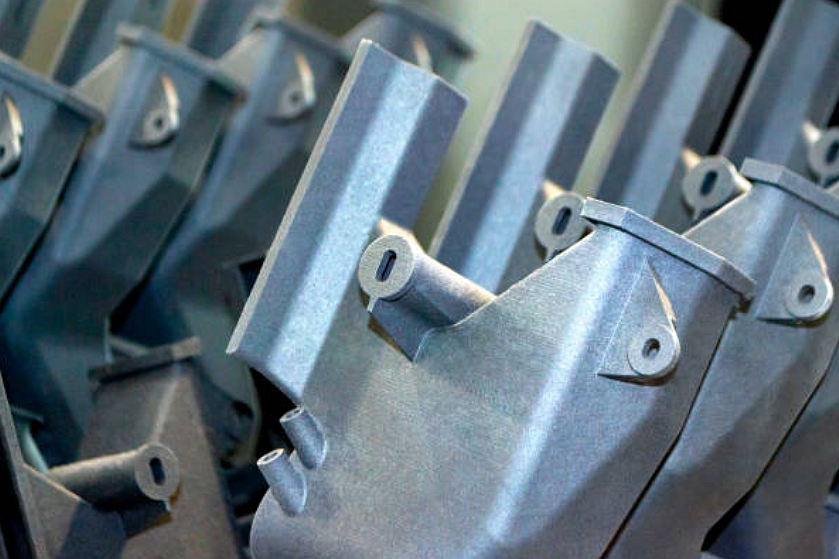
Direct Metal Laser Sintering (DMLS)
The DMLS process begins with preparing a digital 3D model using computer-aided design (CAD) software. The model is then sliced into thin cross-sectional layers, and the DMLS machine uses this data to guide the laser's movement and the application of metal powder. The machine spreads a thin layer of metal powder across the build platform, and the laser precisely scans the layer, selectively melting and fusing the metal particles according to the design specifications.
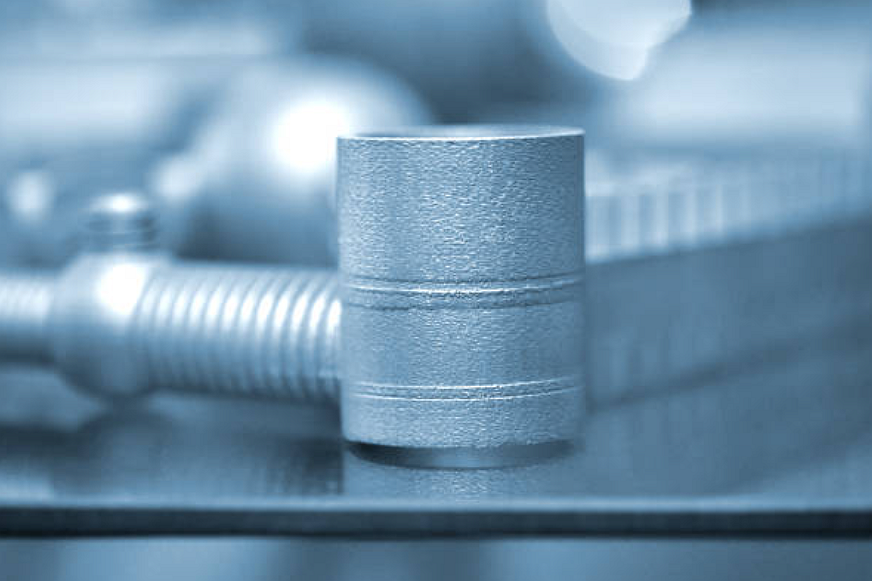
PolyJet
PolyJet works by jetting thin layers of liquid photopolymer materials onto a build tray. Each layer is then instantly cured using UV light to solidify the material. The process repeats, layer by layer until the complete object is formed. What sets PolyJet apart is its ability to mix different materials on-the-fly, creating parts with varying properties, colors, and textures within a single print.
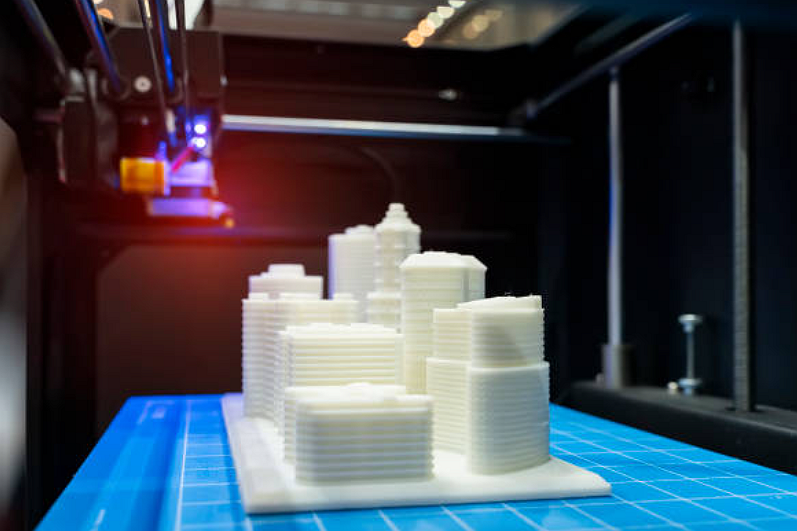
Carbon DLS
Carbon DLS operates by utilizing continuous liquid interface production (CLIP). In this process, a build platform is submerged in a vat of liquid resin. An ultraviolet (UV) image projector projects a sequence of UV images onto the liquid resin, creating a cross-sectional pattern of the printed part. The UV light selectively cures the resin where it is exposed, forming a solid layer.
Using oxygen-permeable optics sets Carbon DLS apart from other 3D printing technologies. A thin layer of oxygen between the liquid resin and the optics prevents the resin from fully curing against the window. This dynamic process allows continuous printing without needing layer-by-layer printing, resulting in significantly faster production times.
Materials Used in 3D Printing
3D printing has evolved beyond its initial stages, and today it encompasses a vast range of materials suitable for different applications. The choice of materials depends on the desired end-use properties, mechanical strength, flexibility, temperature resistance, and aesthetics.
Plastics and Polymers
- ABS (Acrylonitrile Butadiene Styrene): ABS is a widely used thermoplastic known for its strength, impact resistance, and durability. It is commonly used in functional prototypes, automotive parts, and consumer products.
- PLA (Polylactic Acid): PLA is a biodegradable thermoplastic derived from renewable sources such as cornstarch or sugarcane. Printing is easy and finds applications in rapid prototyping, educational settings, and disposable products.
- Nylon: Nylon is a versatile and robust polymer with excellent mechanical properties, high strength, durability, and flexibility. It is commonly used in functional parts, tooling, and engineering applications.
Metals
- Stainless Steel: Stainless steel is a popular metal used in 3D printing, known for its corrosion resistance, strength, and durability. It finds applications in industries such as automotive, aerospace, and medical.
- Aluminum: Aluminum is a lightweight metal with good thermal conductivity and a high strength-to-weight ratio. It is commonly used in automotive components, aerospace parts, and consumer electronics.
- Titanium: Titanium is a lightweight and biocompatible metal known for its excellent strength-to-weight ratio and resistance to corrosion. It is often used in the medical field for implants, aerospace components, and high-performance applications.
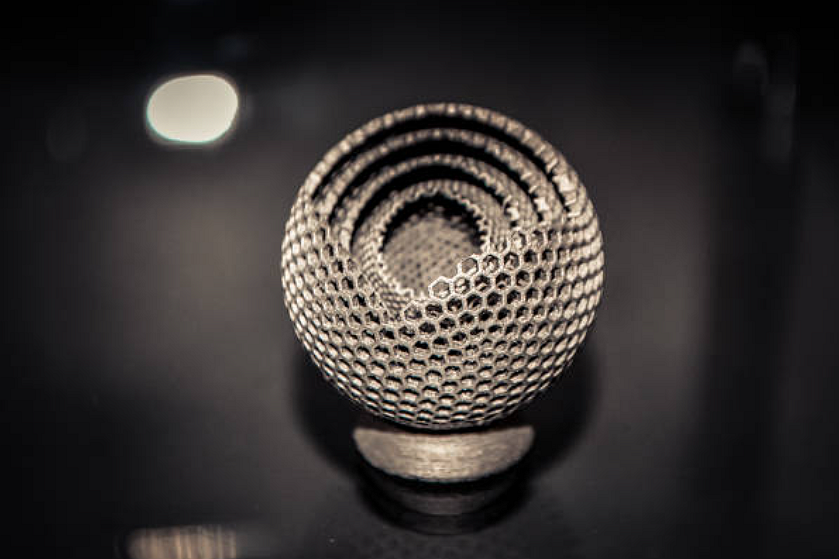
Composite Materials
- Carbon Fiber Reinforced Polymers: Carbon fiber reinforced polymers combine the strength and stiffness of carbon fiber with the versatility of polymers. These materials offer exceptional strength-to-weight ratios and find applications in aerospace, automotive, and sporting goods.
- Glass-Filled Polymers: Glass-filled polymers incorporate glass fibers into a polymer matrix, enhancing the material's stiffness and dimensional stability. They are used in applications requiring improved mechanical properties and resistance to heat and chemicals.
- Metal Matrix Composites: Metal matrix composites combine metals with ceramic or carbon fibers to create materials with enhanced properties such as high thermal conductivity, strength, and wear resistance. They are utilized in industries where lightweight and durable parts are required.
Ceramics
- Porcelain: Porcelain is a ceramic material known for its excellent heat resistance, electrical insulation properties, and smooth surface finish. It finds applications in dental prosthetics, jewelry, and artistic creations.
- Zirconia: Zirconia is a rugged and high-performance ceramic material used in dental applications, such as dental crowns and implants. It offers excellent biocompatibility and durability.
Applications of 3D Printing
The versatility of 3D printing has resulted in its widespread adoption across various industries. Here are some notable applications:
Prototyping and Product Development
3D printing allows for rapid and cost-effective prototyping, enabling designers and engineers to iterate designs quickly and efficiently. It has revolutionized product development, reducing lead times and facilitating innovation.
Medical and Healthcare
The medical field has greatly benefited from 3D printing technology. It enables the creation of patient-specific surgical models and guides, aiding surgeons in planning complex procedures. Customized prosthetics and implants can also be fabricated, providing personalized patient solutions.
Automotive and Aerospace
3D printing has found applications in the automotive and aerospace industries, enabling the production of lightweight parts with complex geometries. This leads to improved fuel efficiency, reduced assembly complexity, and enhanced performance.
Architecture and Construction
3D printing in architecture and construction allows for fabricating intricate building components with greater design freedom. It could revolutionize the construction industry by reducing waste, increasing efficiency, and enabling unique architectural designs.
Fashion and Jewelry
3D printing has significantly impacted the fashion and jewelry industry by offering designers new creative avenues. Customized jewelry pieces and intricate fashion accessories can be quickly produced, providing consumers with unique designs.
Education and Research
3D printing is vital in education and research, allowing students and researchers to visualize complex concepts and ideas. It fosters creativity, problem-solving skills, and hands-on learning experiences.
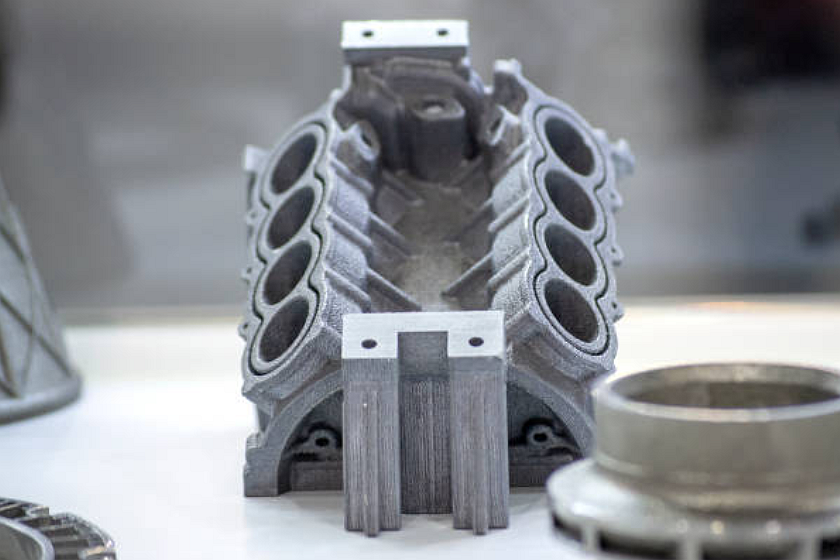
Future Trends and Innovations in 3D Printing
The future of 3D printing is filled with exciting possibilities and ongoing advancements. Here are some trends and innovations to look out for:
Advancements in Materials and Printing Technologies
Researchers continuously explore new materials, including biodegradable polymers, bio-inks for printing human tissues and organs, and advanced metal alloys. Additionally, printing technologies are evolving to improve speed, precision, and surface finish.
Integration of 3D Printing with Other Technologies
3D printing combines other technologies like robotics, artificial intelligence, and virtual reality to create more sophisticated and efficient manufacturing systems. This integration enables automation, real-time monitoring, and improved process control.
Expansion of Applications and Industries
As 3D printing matures, its applications will continue to expand into new industries and sectors. From food printing to space exploration, the possibilities are virtually limitless.
Sustainability and Environmental Impact
3D printing has the potential to contribute to sustainable manufacturing by reducing waste, energy consumption, and transportation needs. As technology progresses, environmentally friendly materials and recycling solutions will become more prevalent.
3D printing has emerged as a transformative technology that reshapes industries and unlocks new possibilities. From the 3D printing process and various technologies to the materials used and diverse applications, this groundbreaking innovation offers unparalleled flexibility, customization, and efficiency. As we look to the future, the continued advancement of 3D printing holds tremendous potential for revolutionizing manufacturing, healthcare, design, and beyond. With each layer printed, we move closer to a world where imagination knows no bounds and the impossible becomes possible through 3D printing.
Why Choose Neway for 3D Printing Service
Are you looking to bring your creative ideas to life? Look no further than Neway, the leading manufacturer of non-standard parts for over three decades. With a wide range of services, including metal, ceramic, and plastic injection molding, precision casting, sheet metal processing, and rapid proofing, Neway is your one-stop solution for all your 3D printing needs. Our state-of-the-art technology and experienced team ensure high-quality and precise output, allowing you to materialize even the most intricate designs. Moreover, we're excited to announce our exclusive promotion for new customers in 2023. Get a head start on your projects with 20% off on your first order with Neway. Take advantage of this incredible opportunity to revolutionize your manufacturing process and experience unparalleled results. Choose Neway for 3D printing and unlock limitless possibilities today!
评论
发表评论