Alumina Al2O3 Material Overview
Alumina Al2O3, also known as aluminum oxide, is a versatile ceramic material widely used in various industries due to its exceptional properties. It is a ceramic compound composed of aluminum and oxygen atoms, characterized by high hardness, excellent thermal and electrical insulation, corrosion resistance, and superior mechanical strength. Alumina Al2O3 is well-known for its ability to withstand extreme temperatures, making it suitable for applications in both high-temperature and cryogenic environments.
Alumina Al2O3 ceramic injection molding (CIM) parts finds applications in diverse industries, including aerospace, automotive, electronics, medical, and chemical. Its exceptional properties make it suitable for use in components such as wear-resistant parts, electrical insulators, cutting tools, substrates for electronic devices, and high-temperature crucibles
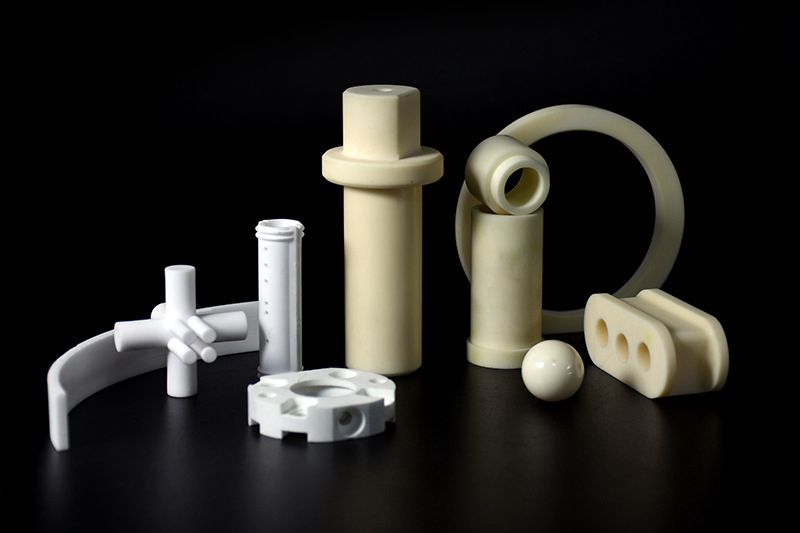
Classification of Alumina Al2O3
In ceramic classification, Alumina Al2O3 ceramics can be classified based on their purity and crystal structure. Purity levels range from 90% to 99.99%, with higher purity grades exhibiting improved mechanical and electrical properties. Crystal structures can be classified into alpha, gamma, and theta alumina, each offering unique characteristics.
Alpha alumina is the most common form and provides excellent mechanical strength, hardness, and wear resistance. Gamma alumina offers enhanced chemical stability and thermal shock resistance, making it suitable for applications involving harsh chemical environments. Theta alumina is a metastable phase with unique properties, primarily used in specialized applications.
Properties and Applications of Alumina Al2O3
Alumina Al2O3 exhibits remarkable mechanical properties, including high hardness, stiffness, and compressive strength. It has low thermal expansion, excellent thermal shock resistance, and exceptional electrical insulation properties. Additionally, it is chemically inert, corrosion-resistant, and biocompatible.
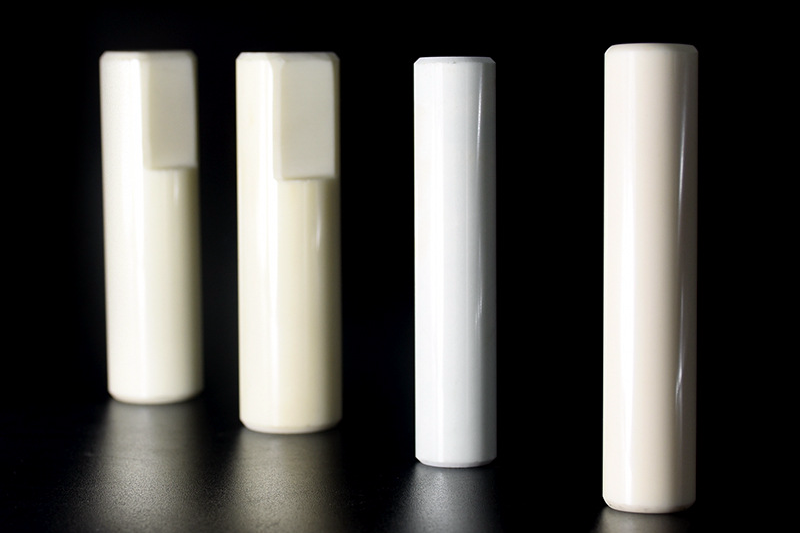
Mechanical properties of Alumina Al2O3
Specific Grade | Density (g/cm³) | Hardness (Mohs) | Compressive Strength (MPa) | Tensile Strength (MPa) | Young's Modulus (GPa) |
---|---|---|---|---|---|
Grade A | 3.97 | 9 | 4000 | 300 | 380 |
Grade B | 3.95 | 8.5 | 3500 | 280 | 360 |
Grade C | 3.90 | 8 | 3000 | 260 | 340 |
Grade D | 3.85 | 7.5 | 2500 | 240 | 320 |
Physical properties of Alumina Al2O3
Specific Grade | Melting Point (°C) | Boiling Point (°C) | Density (g/cm³) | Thermal Conductivity (W/m·K) | Electrical Resistivity (ohm·cm) |
---|---|---|---|---|---|
Grade A | 2072 | 2977 | 3.97 | 30 | 10^14 |
Grade B | 2050 | 2950 | 3.95 | 28 | 10^14 |
Grade C | 2030 | 2927 | 3.90 | 26 | 10^14 |
Grade D | 2010 | 2900 | 3.85 | 24 | 10^14 |
Chemical composition of Alumina Al2O3
Specific Grade | Al2O3 (%) | SiO2 (%) | Fe2O3 (%) | Na2O (%) | TiO2 (%) | CaO (%) | MgO (%) | Other Impurities (%) |
---|---|---|---|---|---|---|---|---|
Grade A | 99.5 | 0.2 | 0.03 | 0.01 | 0.02 | 0.02 | 0.01 | 0.17 |
Grade B | 99.3 | 0.3 | 0.05 | 0.02 | 0.03 | 0.02 | 0.02 | 0.25 |
Grade C | 99.0 | 0.5 | 0.08 | 0.03 | 0.04 | 0.03 | 0.03 | 0.34 |
Grade D | 98.5 | 1.0 | 0.12 | 0.05 | 0.05 | 0.05 | 0.04 | 0.39 |
Alumina Al2O3 ceramics find extensive applications due to their exceptional properties. They are used in the manufacturing of cutting tools, ball valves, pump components, electrical insulators, wear-resistant parts, medical implants, and substrates for electronic devices. The combination of high hardness, wear resistance, and excellent thermal properties makes alumina ceramics ideal for applications that require high performance and reliability.
Preparation of Alumina Al2O3
The preparation of Alumina Al2O3 involves several steps. First, raw materials such as aluminum oxide powders with controlled particle sizes and purities are selected. These powders are then carefully mixed with binders and additives to form a homogeneous feedstock. The feedstock is shaped into the desired form using various molding techniques, including dry pressing, isostatic pressing, and injection molding.
Alumina Al2O3 Ceramic Injection Molding
Alumina Al2O3 can be molded using different techniques, with ceramic injection molding (CIM) being a popular method. CIM allows for the precise and efficient production of complex-shaped ceramic parts with tight dimensional tolerances. The CIM process involves mixing alumina powder with a binder to form a feedstock, which is then injected into a mold cavity under high pressure. After injection, the molded part is carefully debound and sintered to remove the binder and achieve the desired final properties.
Ceramic injection molding offers several advantages over traditional molding methods. It allows for the production of intricate and net-shape components with high precision and repeatability. CIM enables the manufacturing of complex geometries, thin walls, and fine features that are challenging or impossible to achieve using other molding techniques. The process also offers excellent cost efficiency by minimizing material waste and reducing the need for additional machining.
Alumina ceramic injection molding process steps
Feedstock preparation:
Alumina powder is mixed with binders and additives to form a homogeneous feedstock.
Injection molding:
The feedstock is injected into a mold cavity under high pressure using specialized equipment.
Debinding:
The molded part is carefully heated to remove the binders, leaving behind a green body.
Sintering:
The green body is subjected to high-temperature sintering, where it undergoes densification and achieves its final ceramic properties.
Finishing:
The sintered part may undergo additional machining or surface treatments to achieve the desired specifications and aesthetics.
Alumina Al2O3 ceramic injection molding parts exhibit excellent mechanical strength, wear resistance, and dimensional stability. They can withstand high temperatures, making them suitable for applications in automotive engines, semiconductor manufacturing, and cutting tools. The superior electrical insulation properties of alumina ceramics also make them valuable in electronic components, such as insulating substrates and high-voltage insulators.
Alumina Al2O3 ceramic injection molding applications
Cutting tool inserts for machining applications
High-temperature components in gas turbines and engines
Insulating components for electrical and electronic devices
Medical implants and prosthetics
Wear-resistant parts in pumps and valves
Ceramic seals and bearings in various industries
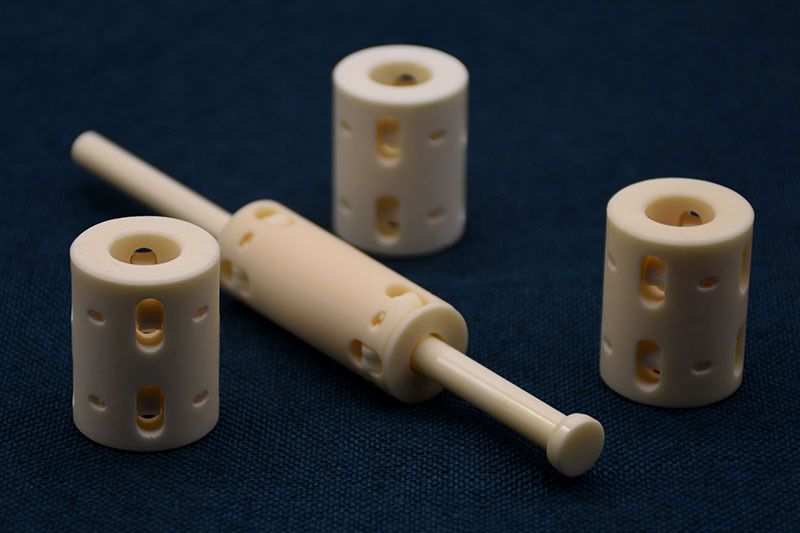
Common Alumina Al2O3 Materials in Ceramic Injection Molding
About injection molded ceramics. In addition to Alumina Al2O3, other materials commonly used in ceramic injection molding include zirconia (ZrO2) and silicon carbide (SiC). These materials offer unique advantages depending on the specific application requirements, such as enhanced toughness, thermal shock resistance, or improved electrical conductivity.
Current Status and Analysis of Alumina Al2O3 Ceramic Injection Molding
The development of Alumina Al2O3 ceramic injection molding suppliers has been advancing rapidly, with a focus on improving material purity, manufacturing processes, and product quality. However, some challenges remain, including the need for better control over material shrinkage during sintering and the development of advanced tooling techniques to achieve higher precision and complexity in molded parts.
The future of Alumina Al2O3 ceramic injection molding looks promising. There is a growing demand for high-performance ceramic components in various industries, driving the need for advanced manufacturing technologies. Ongoing research and development efforts aim to further enhance the properties of Alumina Al2O3 and optimize the ceramic injection molding process for increased efficiency and cost-effectiveness.
Why Choose Neway
Neway is a leading CIM supplier and manufacturer specializing in Alumina Al2O3 ceramic injection molding. With our expertise in material selection, advanced manufacturing capabilities, and dedication to quality, we deliver precision-engineered ceramic parts tailored to meet your specific needs. Experience the benefits of our exceptional products and services with a special offer for new customers - 20% off the first order.
评论
发表评论